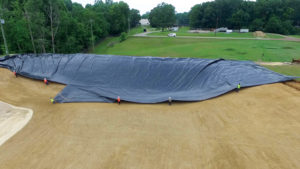
There are more than 100,000 miles (> 160,000 km) of levees throughout the United States, protecting lives and property from extreme weather-related flooding. Aging infrastructure and increasingly stronger storms have intensified the need to reinforce and protect levees, and emergency responders need solutions to repair a breached levee before it results in catastrophic damage. Therefore, in 2009 the U.S. Army Corps of Engineers built a Full-Scale Levee Breach and Hydraulic Test Facility at its Engineer Research and Development Center (ERDC) in Vicksburg, Mississippi. As part of the ERDC’s Coastal and Hydraulics Laboratory, the corps constructed this test facility with three ponds that provide the ability to build and breach full-size levees, and simulate emergency response repair efforts in severe flooding events.
The ponds at the ERDC create a hydraulic system. The lowest-elevation basin catches and stores water permanently but can be pumped to fill the upper (highest-elevation) source basin. The center pond is the test basin where model levees are built, compromised and subsequently repaired during training exercises. During these exercises, water can be released from the source basin and directed through a spillway to the test basin, simulating rising floodwater that threatens the integrity of an earthen levee. At the end of the training, the water returns to the catch basin and is recycled for future use. Since its construction, the facility has been used to successfully test several innovative geosynthetic and composite solutions for sealing and protecting breached levees.
In 2011 the corps recognized the need to preserve the source basin from erosion and seepage. By using a low-grade polyethylene liner that was secured and held together with fabric pins, it could maintain the integrity of the pond for a few years. However, erosion and seepage problems returned along with vegetation and debris accumulation, so the pond became virtually unusable. Levee repair training exercises were postponed while the corps evaluated strategies to make the facility functional again. The corps determined the source basin needed to be returned to its original shape and capacity, and then be lined with an engineered geomembrane to stabilize and protect it for decades of future use (see Figure 1).
A next-generation solution
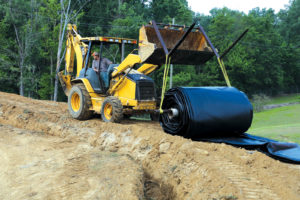
Time and budget constraints led to the opportunity to evaluate the use of an innovative, cost-effective alternative to conventional geomembranes. Instead of selecting a commonly used, unreinforced high-density polyethylene (HDPE) liner, the corps chose a reinforced composite geomembrane (RCG), a 40-mil (1-mm) thick, scrim-reinforced, coated polyethylene base featuring a film laminate surface. Designed specifically for water retention and containment applications, the RCG provided many advantages for the source basin lining project.
“We were very excited to introduce a new geosynthetic solution within this test facility,” said Glenn Myrick of the Coastal and Hydraulics Laboratory and principal investigator for this collaborative research effort. “We can’t wait to have the basins refurbished and available for upcoming research.”
RCGs couple the benefits of traditional woven-coated polyethylene (WCPE) geomembranes with the enhancement offered by a homogeneous film. Alone, WCPE geomembranes provide outstanding tear strength and puncture resistance, but can be challenging to conventionally weld and can exhibit increased water vapor transmission when elongated more than 20%. The addition of a 10-mil (254-µm) low-density polyethylene (LDPE)/linear low-density polyethylene (LLDPE) film laminated to the WCPE base substantially enhances weldability and virtually eliminates inherent permeability. The result is a next-generation geomembrane solution that provides containment performance equivalent to unreinforced HDPE, but with greater ability to resist damage from tears and punctures.
The advantages of the RCG became clear as the need for a high-quality liner installation within a compressed schedule challenged the corps. Due to a scheduled research initiative, there was only a two-week window to prepare the pond and install the liner. The corps hired a contractor to remove the existing damaged liner, vegetation and debris. The contractor also graded, compacted and smoothed the pond subgrade for direct-contact geomembrane placement. The clearing and grading operation on the 1-acre (0.4-ha) source basin was completed in two days, including anchor trench excavation. The pond was ready to be lined.
Fabricating value
Unlike a conventional, unreinforced HDPE geomembrane, an RCG is con-structed in a way that offers the criti-cal advantages of lighter weight, better dimensional stability and exceptional flexibility. Conventional HDPE geomembranes are heavy and rigid, and must be delivered to the project site in rolls that are individually deployed (see Figure 2), and then the seams are welded in place. However, RCGs are lightweight and flexible enough to be seamed into large panels by advanced welding in controlled factory conditions and then folded and rerolled for shipment to the job site. The geomembrane fabricator factory-produced two large RCG panels for installation in the source basin. This allowed the fabricator to accelerate the overall project schedule and enhanced the quality of welds by eliminating issues associated with bad weather, water and mud, slopes and trenches, and temperature fluctuations that come with welding in the field. Once the fabricator
provided a panel diagram (about 10 days in advance of starting the project), the material was ordered, produced and delivered to the site just as the clearing and grading were completed.
“Factory-fabricated geomembranes provide a huge advantage over field-fabricated geomembranes,” said

Dr. Timothy D. Stark, professor of civil engineering at the University of Illinois at Urbana-Champaign and technical director of the Fabricated Geomembrane Institute. “They benefit from higher-quality welds, along with faster and more modular installation to facilitate contractor scheduling.”
Once delivered to the project site, the large panels of fabricated RCG were ready to be installed. The installer had just one week to mobilize, perform the work and demobilize. Deploying the half-acre fabricated panels and welding one connection seam in the middle of the pond was completed in less than one day (see Figure 3).
“These types of geomembranes make installation much easier and faster for my crews,” says Charlie Ellingsworth, vice president of Erosion Control Systems (ECS), the contracted installer for this project. “Knowing that I can have fabricated panels delivered to the site and minimize field welding, I wouldn’t do this any other way.”
The installation crew took advantage of the lighter weight and flexibility of the RCG to complete their work in considerably less time than would have been needed to install a conventional HDPE liner (see Figure 4).
Combating wrinkles and punctures
As the Mississippi sun beat down on the source pond in the early afternoon, another key advantage of the RCG was demonstrated. Conventional unreinforced HDPE liners have high coefficients of linear thermal expansion (CLTE), which result in significant dimensional changes with temperature fluctuations. A 60-mil (1.5-mm) HDPE liner installed on a cool morning may expand several inches in multiple directions by 2 p.m. The consequences are large wrinkles that must be smoothed out before covering with soil or water. Otherwise, HDPE liner wrinkles that fold over on themselves are susceptible to stress cracking and weakening along those folds. The reinforcement scrim plus blended coatings and films of the RCG minimize the thermal expansion and contraction in varied temperatures. RCGs have a lay-flat advantage that eliminates the potential damage that wrinkles can induce.
Perhaps the most significant advantage of an RCG, however, is the ability to resist punctures caused by
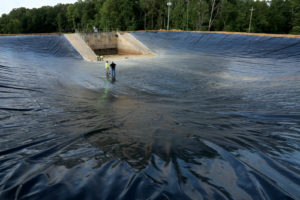
rocks and debris under the liner, along with damage from equipment and wildlife. The composite, layered manufacture of RCGs makes it extraordinarily difficult to poke holes into the liner, which means the potential for leaks is substantially reduced.
“Having geomembrane materials that are free from punctures is critical to performance,” explains Boyd Ramsey, a geo-synthetics consultant. “High puncture-strength values help to prevent damage from both short-term installation stresses as well as longer-term poten-tial penetrations.” Ramsey particularly notes the exceptional puncture strength of RCGs as compared to thicker un-
reinforced HDPE geomembranes.
When the source basin lining was complete, it was clear that the U.S. Army Corps of Engineers made the right choice in selecting an RCG as its geomembrane solution. The containment performance, the quality and ease of both factory and field welds, and the rapid installation all led to the conclusion that RCGs are excellent solutions for water retention and containment applications. Now that the source basin is repaired and operational, testing of rapid repair levee breach solutions can resume at the ERDC.
To view a video featuring the author discussing the installation of the RCG at the ERDC, visit https://tinyurl.com/USACEGeo.
This article has been edited from its original form to list Environmental Protection Inc. (EPI) as the fabricator of the RCG.