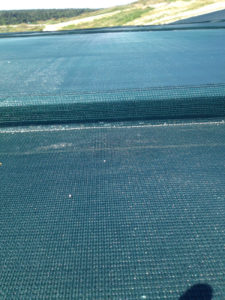
Introduction
Exposed geomembrane cover systems such as rain covers and temporary caps are used on landfills throughout the world. While there are numerous benefits associated with exposed membranes, there are also potential hazards associated with insufficient ballasting or anchoring of the cover materials. For years owners and engineers have used various methods for ballasting exposed geomembranes, including ropes and sandbags, tires, soil windrows, and ground anchors.
Exposed membranes benefit landfills by reducing odors, minimizing leachate production and therefore treatment costs, and providing UV protection to underlying geosynthetics. One of the most significant risks of any exposed membrane cover system is the potential for damage caused by wind loading. Not only can the damaged membrane be costly to repair, but it can be a possible threat to the health and safety of site personnel and property.
Traditional ballasting systems use a point-loading ballast method. Wind uplift occurs as wind blows across the surface of an exposed geomembrane. A recirculating flow of air can create a suction effect on the non-porous geomembrane liner causing it to want to lift. This suction effect can pull the liner off of the ground and could lead to a failed or damaged liner system. Figure 1.1 depicts the conditions that cause wind uplift.
Bethel Landfill
Waste Management’s Bethel Landfill is a solid waste disposal facility located in Hampton, Va. The limits of disturbance for the project encompassed an area of approximately 1,000,000 square feet (sf).
The goal of the project was to remove the existing rope and sandbag ballast system on the existing temporary cap and install an exposed 12-mil rain cover and ballast system. The rain cover and ballast were installed for UV protection of the underlying geosynthetic materials.
The project was completed in stages and the total installation of the rain cover and ballast system took approximately 10 days averaging 100,000sf of rain cover and 100,000sf of ballast material installed per day. The average crew size was 12 throughout the duration of the installation.
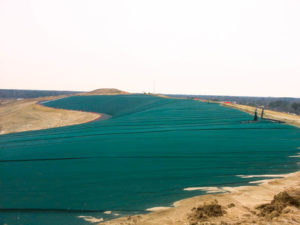
Unlike traditional installations, both the ballast system and the 12-mil rain cover were deployed simultaneously. By installing both materials at the same time, the installer was able to protect the rain cover from any potential damage as well as reducing the overall duration of the installation.
The ballast system panels (328ft × 20ft) were deployed from the top of the slope to the bottom. The material was sewn together via prayer seams, which require a minimum 6-in. overlap to ensure adequate seam strength. A high-strength, UV-resistant thread (277 polyester bonded) was used for long-term strength and durability. After sewing two to four panels together, the installers lined up along the leading edge of the ballast system to hand tension the material. That method of seaming and tensioning was continued throughout the installation process. When reaching the end of a typical work day, the installers would extend the ballast system material past the leading edge of the 12-mil geomembrane and ballast the leading edge with sandbags. This anchored both the ballast system material and the geomembrane overnight to prevent any damage.
Seven months after the 1,000,000sf installation was complete, a few minor repairs were required. Eight areas were repaired because of seam failures and small holes caused by animals. The prayer seams in these areas were pulled apart because of insufficient overlap of the ballast system. The lack of ballast system material above the thread line caused the seams to pull apart while the material was under tension. The holes were patched and the ballast system material was pulled tight, properly overlapped, and restitched. The repairs took less than two hours to complete.
See Figure 1.2, which depicts a correctly executed prayer seam and Figures 1.3, 1.4, and 1.5 for an example of a patched hole.
The 1,000,000sf installation at the Bethel Landfill was completed more than a year ago. The ballast system is performing well and has required only the minor repairs described above.
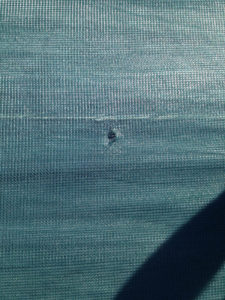
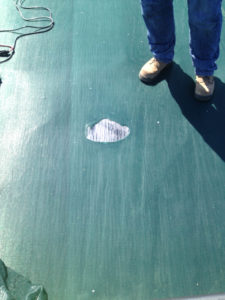
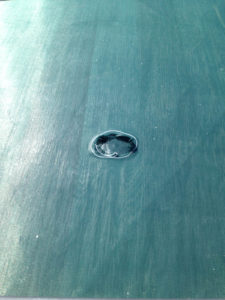
Curley Hollow Landfill
Dominion Virginia Power’s Curley Hollow Landfill is a coal ash disposal facility for the Virginia City Hybrid Energy Center in St. Paul, Va. The limits of disturbance for the project encompassed an area of approximately 80 acres or 3,484,800sf.
The goal of the project was to remove the existing rope and sandbag ballast system and replace it with a new ballast system for UV protection of the underlying geosynthetic materials. The 80-acre project is scheduled for completion during the next four years. A total of 1,087,000sf was installed in 2014.
The initial landfill cell construction utilized a rope and sandbag ballast method on all of the sideslopes. During the winter months, several rope lines failed because of the added weight of the snow on the system and the sandbags slid to the cell floor. This posed a risk to the exposed membrane which was now without a ballast.
Costs to repair the damaged system were high and the client agreed to a 2-acre trial of a new ballast system. During the trial, the site experienced additional rope and sandbag failures and Dominion Power decided to replace their rope and sandbag system completely.
Since the completed installation in 2014, the site has experienced winds in excess of 60mph and the new ballast system has proved to be both reliable and effective.
LCS Landfill
Waste Management’s LCS Landfill is a solid waste disposal facility located in Hedgesville, W.Va. The purpose of this project was to repair a damaged temporary capping geomembrane (8-mil, woven, coated) and replace the failed rope and sandbag ballast system. (See the damaged geomembrane and ballast system in the before photo.)
The limits of disturbance for the project encompassed an area of approximately 50,000sf. An additional goal of the project was to line an existing stormwater channel and ballast the channel lining. The project was completed in 1.5 days in June 2014.