Recognizing design excellence in geosynthetics
The International Achievement Awards, sponsored by the Industrial Fabrics Association International (IFAI), recognize innovation, technical skill and design excellence in geosynthetic applications.
The awards are an annual competition promoting awareness of the specialty fabrics used in thousands of products and applications ranging in size and shape. For more than 70 years, the awards have recognized innovation, technical skill and design excellence. Entries are judged by industry experts, editors, architects, educators and design professionals who were selected for their knowledge in a particular field of study or product area.
The association presented the awards in the Geosynthetics Products competition at IFAI Expo in Dallas, Texas, in mid-October 2018. Categories included Mines/Landfills/Wastewater, Roadways/Infrastructure and Geosynthetics Miscellaneous, including the Best in the Geosynthetics Category overall from TenCate Geosynthetics Americas.
For more information or to enter for the 2019 IAA Awards, visit iaa.ifai.com
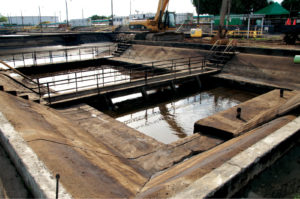
Removal, transport, treatment and final disposal of refinery sewage sludge in Colombia
Project Highlights
Refinery Sewage Sludge Mediation in Colombia
Geosynthetics Producer and Fabricator: TenCate Geosynthetics
Engineer: Nelson Riaño
Installer: GeoSoluciones
Geosynthetics Product: Geotube®
The project was undertaken at the Ecopetrol Refinery at Barrancabermeja, Colombia (Figure 1). The separating unit, in addition to receiving stormwater waste from the industrial area, also converges as “fresh” catalysts of the UOPI cracking unit. According to reports from the refinery operation, this presents problems in the loading process of the hoppers, as well as sludge of the U-2900 water plants, by dragging or disposing of the process units to the rainwater systems. The volume to be pumped was 787,517 cubic feet (22,300 m3), and it took a total of 191 pumping hours. In the end there were 3,000 tons (2,721 tonnes) of dewatered sludge:
- Percent dewatered solids: 50%
- SST effluent: 80 PPM
Geotube 90 × 100 feet (27.4 × 30.5 m)—4 each (Figure 2)
- Circumference: 90 feet (27.4 m)
- Width: 41 feet (12.5 m)—when empty
- Length: 100 feet (30.5 m)
- Fill height: 7.5 feet (2.3 m)
Dewatering cell:
- Length: 115 feet (35 m)
- Width: 197 feet (60 m)
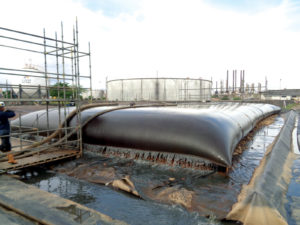
The purpose was to remove the sludge by a pumping system into Geotube units and then allow the sludge to dewater, to lose volume and, finally, to dispose of at the lowest water content possible to a certified landfill. The project featured:
- Work within a refinery
- High standards of safety at work
- Handling and pumping of hazardous waste
- Rainy weather most of the time
- Pumping 1,000 feet (305 m) in distance
- No possibility of entering the lagoons; pumping must be from outside
- High risk of explosion, so a hydraulic pump was to be used (submersible, electric pumps not allowed on-site)
- Having been able to enter a refinery to carry out a job of this type (the first time in Colombia and perhaps worldwide)
- To comply with occupational safety and health standards
- The sewage sludge—a hazardous waste—had to be removed in the cleanest, quickest way; cost is also lower than conventional sludge removal
- Presence of sulfates and CO2
- Mud with traces of oils and crude oil
- Hydraulic unit of the excavator operated the hydraulic pump
- A plant stop—it was necessary to carry out simultaneous operations with other suppliers, which meant meeting daily schedules and deadlines
This was the first time that this method of sludge removal was done in a refinery. The customer said that the previous work always showed problems and serious safety hazards at work, and for the crews who carried out the removal of solids from the separator. This project was done with only a few highly trained people and was completed in one third the time they had estimated, resulting in completing the project at half the budgeted cost.
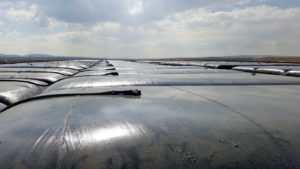
Mogan Lake, Turkey
Project Highlights
Mogan Lake, Turkey
Geosynthetics Producer: TenCate Geosynthetics
Installer: Atlas Maden
Geosynthetics Product: Geotube®
When 95,349,600 cubic feet (2.7 million m³) of sludge needed to be extracted from a 1.5-square-mile (4-km²) eutrophic lake in an urban area by means of a dredge with an hourly minimum capacity of 70,629 cubic feet (2,000 m³), the only appropriate method to reduce the volume by half was by using TenCate Geotube dewatering technology (Figure 3). For its reliable track record of successful large-scale tube dewatering projects, TenCate was selected as system supplier and involved in the choice of the polyelectrolytes, dosing equipment, hydraulic layout, the design of the dewatering cell and the training of on-site personnel.
The project aims to put an end to the eutrophic state of the lake that was overgrown with water plants, suffered from cyanobacterial blooms, chlorophyll and nutrients, causing a bad smell. Due to these poor conditions, it could not be used recreationally by the population.
To extract the sediments without causing stronger smell and without disrupting the nature reserve, the authorities opted for hydraulic dredging. Using this environmentally friendly method meant that the sludge was dissolved in more water, increasing the volume to be dredged to more than 281 million cubic feet (8 million m³).

The uniqueness of this project resides in the way that volume was handled using geosynthetics. Indeed, to treat this kind of volume effectively in a relatively short time, geotextile tube dewatering is the only option. To receive more than 70,629 cubic feet (2,000 m³) per hour of dredged material, TenCate proposed a design for a dewatering cell on a footprint of no more than 0.04 square mile (0.1 km²) on which 4 × 140 tubes rapidly filtered out the solids while the particle-free effluent water was guided off-site to flow back to the lake (Figure 4).
Using Geotube bags saved millions of dollars and mitigated the release of CO2 on a large scale compared to mechanical dewatering. It effectively prevented the development of smell, erosion and long-term occupation of farmland in comparison to decantation basins. The project is in its last stages, and already the aquatic life in the lake is visibly improved; clearer water and more fish can be observed. When the last bags are removed, the temporary occupation of the area will be finished and will be restored to its original status.
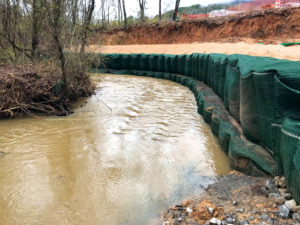
Mountain Creek shoreline restoration in Tennessee
Project Highlights
Mountain Creek Shoreline Restoration, Tenn.
Geosynthetics Producer and Fabricator: Propex Geosynthetics
Engineers: Chattanooga Engineering Group
Installer: Wright Brothers Construction
Geosynthetics Products: SCOURLOK Shoreline Defense System, ARMORMAX slope stability system
A severely eroded section of Mountain Creek near Chattanooga, Tenn., jeopardized the structural stability and safety of Red Bank Elementary School’s access road and outdoor nature classroom. To restore the streambank and stabilize the eroded slope above it, a 105-foot (32-m) section of the stream needed an engineered and sustainable solution.
To restore the streambank, stabilize it to resist future erosion and provide a sustainable solution, a combination of SCOURLOK and ARMORMAX Engineered Earth Armoring Solutions was used. SCOURLOK is a new vegetated shoreline defense system developed by Propex (Figure 5). It is designed to resist extreme hydraulic stresses to help protect streambanks, shorelines and other similar applications while promoting vegetation in lieu of hard armor. Additionally, it provides water-quality benefits, including pollutant and nutrient removal. ARMORMAX was used to stabilize the slope above the streambank to prevent erosion from larger flood events. This system combines geotextiles and a high-performance turf reinforcement mat with engineered earth anchors to provide surficial slope stability.
Mountain Creek flows through the community of Red Bank, Tenn., to the Tennessee River. It has been identified by the Tennessee Department of Environment and Conservation (TDEC) as a 303(d)-listed stream, meaning that its pollution exceeds the state’s standards for one or more water-quality criterion. Habitat alteration and sediment have been identified as the main pollutants, and they are due, in part, to channel erosion caused by urban development and increased stormwater runoff. Previous studies conducted on the Mountain Creek watershed have indicated that erosion of the Mountain Creek stream channel is estimated to be between 66% and 81%. The purpose of the project was to reinforce the creekbank, stabilize the slope leading from the school’s access road to the creek, improve water quality in the watershed and protect the school’s outdoor nature classroom.
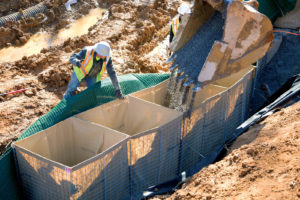
This restoration project was spearheaded by TenneSEA (Tennessee Student Environmental Alliance), a Chattanooga organization that collaborates with communities to teach children about their connection to nature. TenneSEA reached out to Red Bank Elementary School alumni who are involved in floodplain management, stormwater control, and the erosion prevention and sediment control (EPSC) industry. A collaborative team of local businesses, nonprofit organizations, school staff and government agencies donated their time and resources to tackle the project.
Students at Red Bank Elementary School also played a part by participating in the Stream Team, a program that teaches students about the natural world around them by using real-world problems while determining sustainable solutions. Students learned about watersheds, flooding, EPSC and water quality, and they assisted in engineering design and construction oversight.
Construction began in early December 2017 and was completed in January 2018. A total of 105 feet (32 m) of streambank and the above slope were successfully restored and stabilized (Figure 6), protecting Red Bank’s access road, preventing additional sediment from being deposited in an impaired watershed and, most importantly, providing a safe outdoor nature classroom where students can continue to take part in restoration efforts of the Mountain Creek watershed.
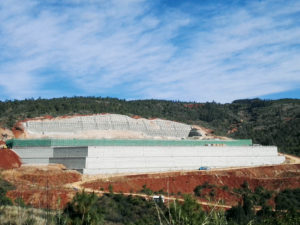
Geotextile-reinforced soil retaining wall for MSW plant in China
Project Highlights
Geotextile Reinforced Soil Retaining Wall in China
Geosynthetics Producer and Fabricator: TenCate Geosynthetics
Installer: Yunnan Construction and Investment Holding Group
Geosynthetics Product: Mirafi
The Yuxi Municipal Solid Waste Incineration and Power Generation Plant is a $50 million investment to manage the collection and incineration of municipal solid waste (MSW) in a rural area of China. The incinerator will operate at a temperature of 1,472˚F (800˚C), which reduces the MSW to ashes, and the associated heat energy generated will be converted to electricity using steam-powered turbine generators. The site is located on rugged terrain at an elevation of 5,906 feet (1,800 m) in Yunnan Province.
The project involves the construction of a 108-foot (33-m) high, multitiered geotextile reinforced soil retaining wall to create leveled platforms for the plant (Figure 7). Each tier consists of 984–1,148-foot (300–350-m) long and 26-foot (8-m) high near-vertical wall facings. The client wanted a solid-looking retaining wall that could withstand tremors in this earthquake-affected area. As the area is not easily accessed during construction, the client also wished to have a wall system that requires minimal importation of materials, avoids use of special construction equipment and does not require specialist skills for erection of a wall. The Mirafi reinforced soil retaining wall system fit the request. The wall system uses geotextile reinforcement to reinforce the locally available soil and is constructed as earthworks are carried out. It is well known to the industry that a geotextile-reinforced soil retaining wall outperforms rigid wall systems, such as conventional reinforced concrete retaining walls, during earthquakes.
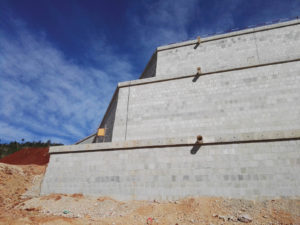
Modular concrete blocks are used to provide a solid facing for the retaining wall (Figure 8). The blocks can be made using an on-site or off-site wet-casting method using repetitively used steel molds. The facing block unit measures 1.3-feet (0.4-m) wide, 1.3-feet (0.4-m) high and 1.6-feet (0.5-m) deep and has tongue-and-groove features at the bottom and the top of the block respectively. The facing block can be handled manually, and the tongue of the upper block fits into the groove of the lower block, which mechanically locks in the interlaid geotextile reinforcement to the facing units. Backfill is placed in compacted layers using local excavated soil behind the facing blocks. Mirafi SR2500 reinforcement geotextile is laid in vertical spacing of 1.3 feet (0.4 m), which corresponds to the tongue-and-groove interlocking levels of the modular facing blocks. The length of reinforcement geotextile extends behind the facing blocks up to a maximum of 79 feet (24 m), depending on the design.
The TenCate Mirafi reinforced soil retaining wall system is unique because, apart from normal earthwork machinery for the backfilling and compaction of soil, the laying of Mirafi geotextile reinforcement and the placement of modular concrete blocks can be done manually while achieving very exacting fascia profiles and aesthetics. The wall system required only transportation of Mirafi SR geotextile reinforcement and modular concrete blocks to the site. The lightweight Mirafi SR geotextile reinforcement and the modular concrete blocks form a small fraction either by volume or by weight, when compared with that of the concrete, steel and formwork needed for a conventional concrete retaining wall. This is a huge advantage for construction of retaining walls in rural environments. As the site is on rugged terrain, a modular block facing can conform to the ground contours much more easily than conventional cast-in-place reinforced concrete retaining wall options.
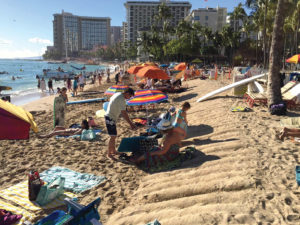
Waikiki Beach Sand-Filled Mattress
Project Highlights
Waikiki Beach Sand-Filled Mattress
Geosynthetics Producer: TenCate Geosynthetics
Engineer: Dolan Everson
Installer: Geotech Solutions
Geosynthetics Product: Geotube®
In December 2017 the City of Honolulu and the Waikiki Beach Association funded a program to install Geotube sand-filled mattresses as an innovative solution to protect critical areas of Waikiki Beach affected by erosion (Figure 9). Sand-filled mattresses are two layers of geotextiles sewn together to form longitudinal chambers that are filled with sand slurry. The bottom layer is a high-strength woven polypropylene geotextile. The top layer is a composite consisting of a woven polypropylene geotextile with a 3-inch (8-cm) thick layer of highly UV-stabilized crimped fiber needled into the top surface. When installed, this sand-colored fiber traps and holds sand providing a natural surface appearance. This was a critical requirement for any erosion protection installed on Waikiki Beach. The distributor in Hawaii—Geotech Solutions—and the City of Honolulu Parks Department personnel, installed the 200-foot (61-m) long section of sand-filled mattresses in two days and opened the beach to the public for use. Based on the performance, a second mattress section was installed on another Hawaiian beach the following month.
The purpose of the project was to restore the natural appearance of this section of Waikiki Beach and to provide a safe environment for tourists to enjoy the beach.
The City of Honolulu and the Waikiki Beach Association requested that the erosion restoration and protection provide a natural appearance and safe surface of the beach.
All the sand had been eroded from this section of Waikiki Beach and only clay and rocks were on the surface. This section of beach had an unappealing appearance and was not safe for use. The sand-filled mattress has a top surface of soft sand-colored fiber that traps sand particles and takes on a natural sand beach appearance that blends into the existing environment.
The day after the sand-filled mattress was installed, tourists were lying on the newly restored beach and could not perceive the difference.