Nicknamed Project Redtail, the construction of a sprawling 660,000-square-foot (61316 sq m) online retail logistics center and supporting infrastructure in East Fishkill, N.Y., demanded the utilization of nearly every inch of the parcel hosting the facility.

A hybrid mechanically stabilized earth (MSE) and gravity wall allowed the project to navigate a difficult property line, maximize the site’s available space, and keep the construction of the vital regional economic development effort on schedule.
To gain the square footage necessary for the construction of the logistics center, Project Redtail’s plans called for a wall along the main entrance road to the facility and tight to the property line of a parcel owned by a regional power company. Guy-wires were stabilizing utility poles within the wall’s proposed construction footprint and the wall itself infringed on the power company’s property by several feet.
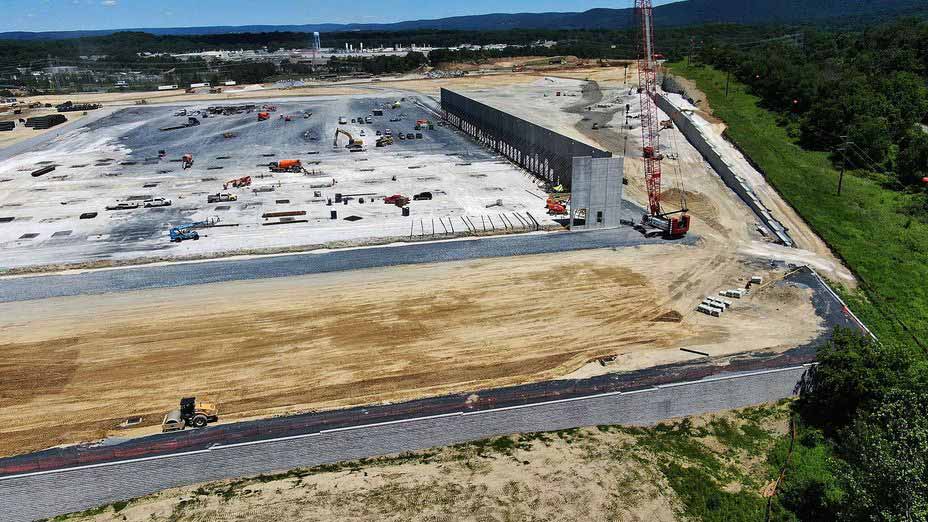
The wall design consisted of both MSE and gravity systems. New York’s Hudson Valley Redi-Rock manufacturer Mid-Hudson Concrete Products supplied 28-inch (710 mm) Positive Connection (PC) blocks with geogrid to form the MSE portion of the wall. MSE (or reinforced) blocks utilize anchors behind the wall – typically geogrid or earth anchors – to engage the weight of the backfill soil, adding additional stability to the wall. Finishing the wall were 28-inch (710 mm) Solid blocks which leverage the mass of the blocks themselves to retain the earth without the need for additional reinforcement. The hybrid design ultimately produced a wall engineered and installed specifically to the project’s needs.
Petillo New York LLC – part of the Petillo Construction family of companies, one of the northeast’s leading heavy construction firms – was contracted to build both the warehouse and the retaining wall. Petillo’s first order of business was to secure an easement from the power company to relocate the guy-wires and allow for the installation of the wall as proposed.
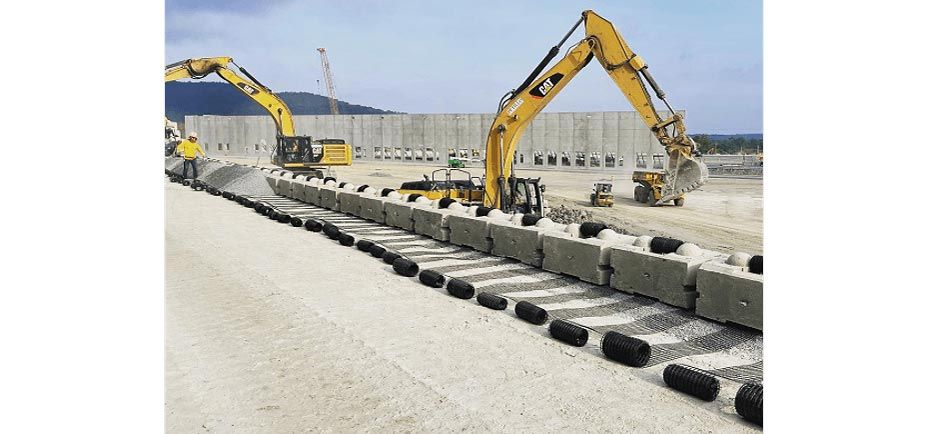
While the immediate utility and property line issues had been resolved, the proposed wall’s proximity to the neighboring property demanded a minimally intrusive installation. The expansive Redi-Rock block library includes multiple product options. These can be easily combined to build hybrid walls, providing wall designers and installers the flexibility to control the earth utilizing multiple block types working in concert with one another.
Petillo Construction engaged Mid-Hudson Concrete Products previously to supply a 24,000-square-foot (2230 sq m) wall for a high-profile casino project, so the installer was familiar with both the technology of the product and the reliability of the manufacturer. The logistics facility wall measures 1,770 feet (539.5 m) long and stands an imposing 33 feet (10 m) tall. Its 34,000-square-foot (3158 sq m) surface area makes it the most extensive single-wall system Petillo Construction has installed to date.
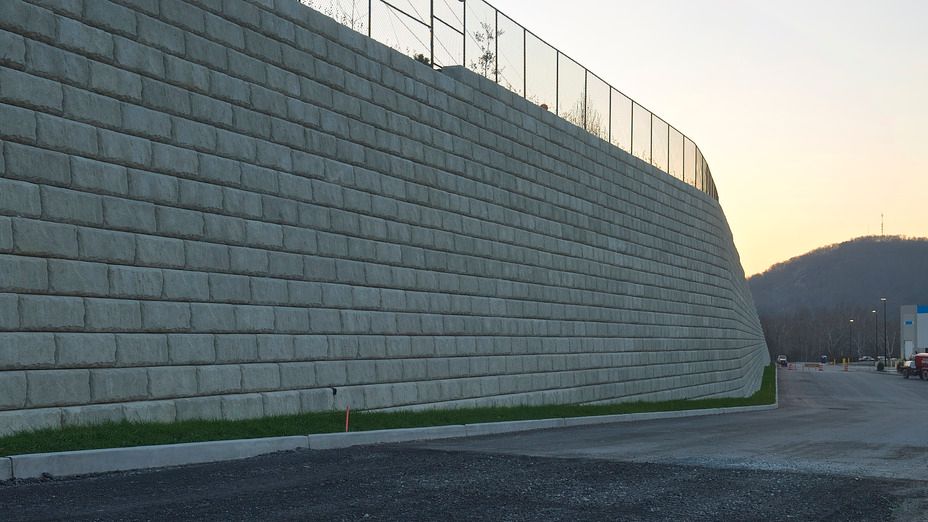
Installing initial courses of reinforced blocks and then finishing the top of the wall with a gravity solution allowed Petillo Construction to achieve the height, stability, and look they needed while limiting the use of space behind the wall and reducing associated excavation and backfilling.
The construction of the enormous distribution center was a tall order, considering the need to maximize limited available land and navigate easement challenges that initially threatened the project’s viability. Project engineers utilized Redi-Rock to help them overcome both hurdles by erecting a vital retaining wall within a severely restricted footprint and delivering the solid solution Project Redtail demanded right when it was needed.

Upon completion, the distribution center is expected to create more than 500 full-time jobs and up to 700 part-time positions while generating significant tax revenues for regional schools, libraries, and infrastructure. The construction process alone is anticipated to require more than 300 temporary positions.
Article originally posted on Redi-Rock.com. Learn more about Redi-Rock here.