By Ben Campbell, P.E., Propex
Earth anchors come in all shapes and sizes and are made from a variety of materials including steel, aluminum, stainless steel and ductile iron. Earth anchors are also used for many different purposes. Propex primarily uses percussion-driven engineered earth anchors (EEA) to create an artificial deep root system for ARMORMAX. The ARMORMAX system is composed of EEAs that are designed and tested for compatibility and performance with our high-performance turf reinforcement mats (HPTRM). This system is used to provide surficial slope stabilization and erosion control for up to 75 years.
More than 35 million square yards (32 million m2) of our HPTRM span the globe, with installations in nearly every region of the world. ARMORMAX was designed to be a versatile system that can be adapted to address different site conditions and challenges. For example, soil conditions in Tampa, Fla., are much different than soil conditions in Tucson, Ariz. Understanding site conditions for each installation, as well as the project goals, will help determine which type of EEA to use. To adapt to various site conditions and challenges, Propex has engineered three different anchor sizes.
Most erosion prevention applications require a limited amount of pullout capacity, around 200–300 pounds (91–136 kg), and include loose soils. A B1 anchor is commonly used in these conditions. In contrast, a slope stability project may require a pullout capacity of 1,500 pounds (680 kg) or more. This project would require a larger anchor with a greater embedment depth, such as a B2 or B3.
Projects that have very rocky soils, or even ones that consist of highly weathered rock such as shale, require a much stronger anchor that is made of something like ductile iron. Subsurface conditions that consist of a shallow (10 feet [3 m] or less) layer of competent rock, such as granite, are not ideal applications for a percussion-driven EEA. Anchors for this type of condition would need to be drilled.
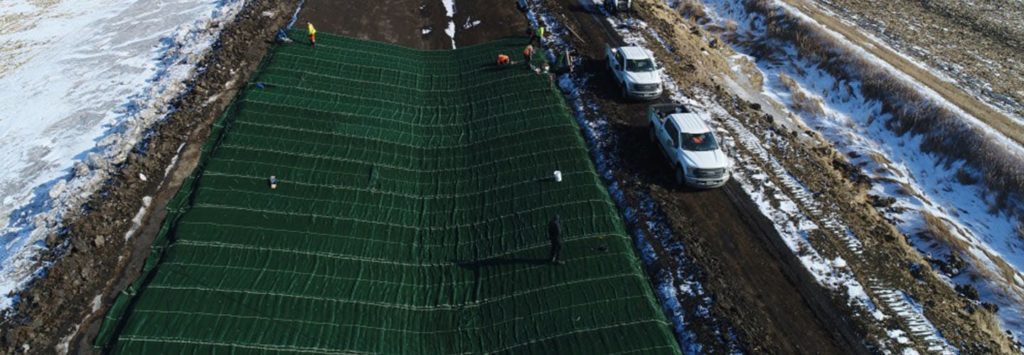
Occasionally, EEAs must be driven through the frozen ground. Most ARMORMAX projects are not installed during the winter, however, project conditions can cause delays that push installation into the winter months. A great example is the Reinland Drainage Channel that was installed in Manitoba, Canada. Due to wet weather, the construction schedule was delayed until the winter months. This delay caused major challenges including installing anchors in frozen ground.
Because the ground freezes from the surface down, the longer the schedule stretches into the winter, the deeper the layer of frozen ground becomes. This is where the fun part begins. In many cases, a pilot hole can be drilled with a 12–18-inch (30–46-cm) bit that has a slightly larger diameter than the anchor. Even though EEAs are driven a minimum of 3 feet (0.9 m), the pilot hole only needs to be drilled to a depth past the layer of frozen ground. Pro tip: Once the ground’s frozen layer reaches 18–24 inches (46–61-cm), it is best to place the project on hold until spring. The frozen ground will inherently provide erosion prevention by itself.
As with most products that we purchase in our daily lives, the larger and stronger they are, the more expensive they are. As an engineer, it is most important to never underspecify. This could put the health, safety and welfare of the public and the environment at risk. It is also important to provide the owners of our projects with exceptional value and avoid significantly overspecifying components on projects.
This article original appeared on the Propex blog, https://propexglobal.com/company/whats-new.